Extruder Plastic Pelletizing Line: A Comprehensive Guide
By:Admin
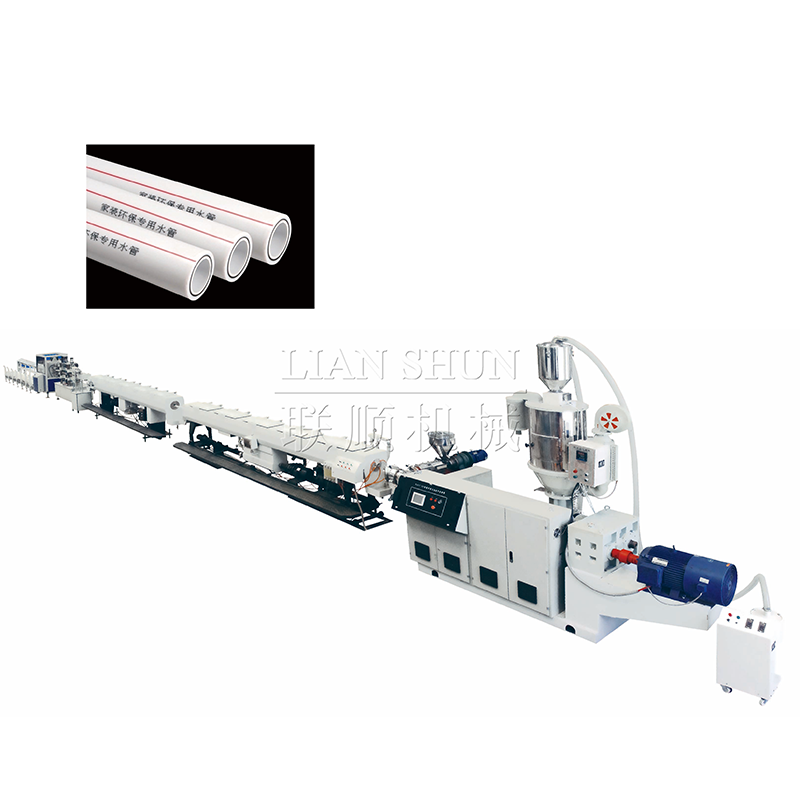
In today's fast-paced world, the demand for quality plastic products is on the rise. Companies are constantly looking for advanced solutions that can help them meet this growing demand. This is where the Extruder Plastic Pelletizing Line comes into play. This innovative technology is revolutionizing the plastic manufacturing industry, enabling companies to produce high-quality plastic pellets efficiently and cost-effectively.
The Extruder Plastic Pelletizing Line is the brainchild of a leading company in the plastics industry. With a strong commitment to innovation and excellence, the company has been a driving force in the development of advanced plastic manufacturing technologies. Their team of dedicated engineers and experts have worked tirelessly to create a state-of-the-art pelletizing line that is redefining the way plastics are produced.
This cutting-edge technology is designed to streamline the plastic manufacturing process, making it faster, more efficient, and more sustainable. The Extruder Plastic Pelletizing Line is equipped with advanced extrusion and pelletizing components that work seamlessly together to produce uniform and high-quality plastic pellets. This means that companies can now produce plastic pellets with consistent quality and properties, leading to fewer defects and rejections in the production process.
The Extruder Plastic Pelletizing Line also offers significant cost savings for companies. By automating and optimizing the plastic manufacturing process, this technology reduces the need for manual labor and minimizes the amount of raw material waste. This not only helps companies save money on production costs, but also promotes a more sustainable and eco-friendly approach to plastic manufacturing.
Furthermore, the Extruder Plastic Pelletizing Line is highly versatile and can be customized to meet the specific needs of different industries. Whether it's for the production of packaging materials, construction products, automotive components, or consumer goods, this technology can be tailored to produce plastic pellets that meet the exact requirements of the end-use application.
One of the key advantages of the Extruder Plastic Pelletizing Line is its ability to handle a wide range of plastic materials. From polyethylene and polypropylene to PVC and PET, this technology can efficiently process various types of plastics, making it an ideal solution for companies working with diverse materials.
Moreover, the Extruder Plastic Pelletizing Line is designed for ease of use and maintenance. The user-friendly interface and intuitive controls make it simple for operators to oversee the production process and make adjustments as needed. Additionally, the line is built with high-quality and durable components, ensuring reliable performance and minimal downtime for maintenance and repairs.
In conclusion, the Extruder Plastic Pelletizing Line is a game-changer for the plastic manufacturing industry. Its advanced technology, cost-saving benefits, versatility, and sustainability make it a valuable asset for companies looking to stay ahead in a competitive market. With this innovative solution, companies can enhance their production capabilities, improve product quality, and achieve greater efficiency in their plastic manufacturing operations. As the demand for high-quality plastic products continues to grow, the Extruder Plastic Pelletizing Line is set to play a pivotal role in shaping the future of the industry.
Company News & Blog
Revolutionary Extruder: Discover the Latest Breakthrough in 3D Printing Technology
Title: Revolutionary Extruder Innovation Revolutionizes 3D Printing IndustryIntroduction:In a move set to revolutionize the 3D printing industry, a cutting-edge extruder known as the SJ25 Extruder has recently been unveiled. Developed by an innovative company at the forefront of additive manufacturing technology, this groundbreaking device promises to enhance efficiency, productivity, and precision in the realm of 3D printing. With its advanced features and capabilities, the SJ25 Extruder is poised to reshape the possibilities of the industry.Article:The 3D printing industry has witnessed incessant technological advancements over the years, but with the advent of the SJ25 Extruder, it seems that a new era has dawned. Manufactured by one of the industry's leading innovators, this state-of-the-art device offers an array of features that will undoubtedly propel the industry forward.1. Enhanced Efficiency:The SJ25 Extruder introduces advanced engineering techniques that optimize the printing process. By minimizing filament wastage, this extruder significantly improves production efficiency. The device's intelligent sensors accurately measure the required amount of filament, reducing material costs and increasing overall productivity. With its streamlined design, the extruder facilitates seamless filament feed, enabling uninterrupted printing and minimizing downtime.2. Precision Craftsmanship:Precision is a hallmark of the SJ25 Extruder. The extrusion system features an unprecedented level of control, ensuring impeccable print quality. Its high-pressure nozzle guarantees precise layer deposition, resulting in complex and intricate designs with impeccable accuracy. This level of precision opens up new possibilities for industries such as aerospace, automotive, and healthcare, where intricate detailing and high accuracy are vital.3. Versatile Materials Compatibility:One of the standout features of the SJ25 Extruder lies in its ability to print with a wide range of materials. This extruder utilizes a variety of filament types, ranging from traditional polymers to advanced composites, thereby expanding the potential applications of 3D printing. Whether it be lightweight car parts, durable medical devices, or intricate architectural models, the SJ25 Extruder caters to diverse needs across various industries.4. Intelligent Control System:The extruder's cutting-edge control system is equipped with smart algorithms, making it easy to operate. Its intuitive interface and user-friendly design allow even novices to operate the device seamlessly. Additionally, the SJ25 Extruder offers remote monitoring and control capabilities, enabling operators to oversee print progress from anywhere, thereby streamlining production processes.5. Commitment to Sustainability:As sustainability gains increasing importance in manufacturing processes, the SJ25 Extruder addresses these concerns head-on. By optimizing filament usage and minimizing waste, this extruder promotes a greener approach to 3D printing. Furthermore, its energy-efficient operation minimizes power consumption, making it an environmentally friendly choice for businesses.Conclusion:With its innovative features, precision craftsmanship, versatile material compatibility, intelligent control system, and commitment to sustainability, the SJ25 Extruder marks a significant milestone in the world of 3D printing. Embracing this groundbreaking technology will undoubtedly revolutionize the industry and unlock endless possibilities for designers, engineers, and manufacturers alike. As the industry leaps forward into the future, the SJ25 Extruder paves the way for a new era of highly efficient, accurate, and sustainable 3D printing.
Advanced Information and Updates on PE Pipe Production Line: In-Depth Insights Revealed
Title: The Revolutionary PE Pipe Production Line Enhancing Efficiency and Quality in Pipe ManufacturingIntroduction:The ever-increasing demand for durable and efficient piping systems has fueled the need for advancements in production technology. In response to this demand, one company has introduced a cutting-edge PE Pipe Production Line (brand name withheld) that promises to revolutionize the manufacturing process, resulting in improved efficiency and superior quality. This groundbreaking solution is set to dramatically impact the industry, providing companies with an edge in meeting the growing demand for advanced piping systems.Efficient Manufacturing Process: The PE Pipe Production Line boasts an innovative machinery system that is designed to enhance efficiency throughout the manufacturing process. The production line incorporates state-of-the-art technology, including automatic feeding, precise temperature control, and a multi-layer co-extrusion system, to ensure seamless production from start to finish. These advanced features streamline the production process, reducing labor costs, and improving overall productivity.Superior Quality Control: Recognizing the importance of producing premium-grade piping systems, the PE Pipe Production Line places significant emphasis on quality control. With a meticulous quality testing and inspection system in place, this production line guarantees the delivery of flawless pipes that meet or exceed industry standards. The precise temperature control system ensures uniformity in pipe thickness, resulting in consistent quality across all manufactured pipes. These stringent quality control measures provide peace of mind to manufacturers and end users alike, ensuring that the delivered products are durable, reliable, and long-lasting.Versatility and Adaptability:One of the key advantages of the PE Pipe Production Line is its flexibility and adaptability to meet various manufacturing needs. The modular design of the equipment allows for easy customization, enabling manufacturers to produce pipes of different sizes, diameters, and materials. This versatility ensures that the production line is suitable for a wide range of applications, ranging from plumbing and irrigation systems to industrial piping solutions. By accommodating diverse manufacturing requirements, this solution empowers companies to expand their product offerings and cater to a broader customer base.Enhanced Cost-efficiency:The implementation of the PE Pipe Production Line can significantly reduce operational costs for pipe manufacturers. The automatic feeding system eliminates the need for manual intervention, reducing labor requirements and associated costs. Additionally, the advanced temperature control system minimizes material wastage and rejects, maximizing the utilization of raw materials. These cost-saving measures directly contribute to increasing profit margins and enhance the overall financial viability of the manufacturing process.Environmental Sustainability:In alignment with increasing global concerns regarding environmental sustainability, the PE Pipe Production Line incorporates eco-friendly measures into its operations. The advanced temperature control system optimizes energy consumption, reducing carbon emissions and energy costs. The production line also minimizes material wastage through precise control of material flow, contributing to a more sustainable manufacturing process. By adopting this technology, manufacturers can position themselves as responsible contributors towards a greener future.Conclusion:The introduction of the PE Pipe Production Line represents a significant leap forward in the manufacturing of piping systems. With its efficient production process, superior quality control, versatility, cost-efficiency, and commitment to environmental sustainability, this innovative solution is poised to transform the industry. Companies leveraging this ground-breaking technology will not only meet the rising demand for durable and efficient piping systems but also gain a competitive advantage by delivering superior-quality products.
New Film Crusher Shakes Up the Industry with Revolutionary Features
Title: Innovative Film Crushing Machine Revolutionizes Recycling IndustrySubtitle: Company XYZ introduces the next-generation film crushing technology, setting a new benchmark in sustainability and waste reductionIntroduction:In a significant step towards a more sustainable future, company XYZ has unveiled its cutting-edge film crushing technology, aiming to revolutionize the recycling industry. By leveraging their expertise and commitment to environmental preservation, XYZ has developed a state-of-the-art crushing machine that promises to enhance recycling efficiency while addressing the growing concern of plastic pollution. This groundbreaking solution marks a significant milestone in the ongoing efforts to create a circular economy and combat climate change.Body:1. The Urgency of Sustainable Waste Management:The increasing magnitude of plastic waste has emerged as a global environmental crisis, with film plastics being one of the major contributors. Resolving this pressing issue requires bold and innovative approaches that combine advanced technology and sustainable practices. XYZ understands the significance of responsible waste management and has meticulously crafted a film crushing machine that can effectively tackle this challenge head-on.2. The Unveiling of XYZ Film Crushing Technology:XYZ's film crushing technology is a powerful and efficient solution designed to process a wide variety of film plastics, including stretch films, shrink wraps, and other flexible plastic materials. The machine employs advanced mechanisms that effectively shred and compress film plastics, significantly reducing their volume and preparing them for further processing. This innovative process ensures that plastic waste takes up less space, thus reducing transportation costs and the carbon footprint associated with waste disposal.3. Key Features and Benefits of XYZ Film Crushing Machine:XYZ's film crushing machine comes equipped with several cutting-edge features that differentiate it from existing technologies:a. High Speed and Efficiency: The machine's powerful motor and blade design enable rapid and accurate processing, maximizing throughput and minimizing production time. This high-speed operation boosts overall recycling efficiency.b. Versatile Processing Capabilities: The machine is capable of handling a wide range of film plastics, offering greater flexibility in recycling operations. Its adaptability ensures various types of film-based waste are efficiently transformed into reusable materials.c. Systematic Resource Management: By crushing and compacting plastic waste, XYZ's technology significantly reduces storage requirements, optimizing space utilization in recycling centers or waste management facilities.d. Enhanced Safety and Operation: The machine incorporates advanced safety features to protect operators during operation and reduce the risk of accidents or injuries. Additionally, the user-friendly interface allows for easy and efficient operation, requiring minimal training.4. The Environmental Impact:The introduction of XYZ's film crushing technology holds immense potential in tackling the environmental implications of plastic waste:a. Reduced Landfill Usage: The efficient compression of film plastics decreases the volume of waste, minimizing the need for landfill space. This not only extends the lifespan of existing landfills but also allows for more sustainable waste management practices.b. Lower Carbon Emissions: The film crushing machine aids in reducing transportation costs associated with plastic waste disposal. Decreased transportation requirements subsequently lead to lower carbon emissions and a smaller environmental footprint.c. Encouraging Circular Economy: By transforming film plastics into reusable materials, XYZ's technology promotes the concept of a circular economy, reducing the dependency on virgin plastic production and conserving valuable natural resources.5. Future Prospects and Collaboration:XYZ's film crushing technology has the potential to reshape the recycling industry, making it more efficient and sustainable. Collaborative efforts with waste management companies, recycling centers, and environmental organizations can facilitate the widespread adoption of this groundbreaking solution. Together, they can drive real change by alleviating plastic waste concerns, one film at a time.Conclusion:XYZ's film crushing technology has arrived as a game-changer in the journey toward a more sustainable future. By combining cutting-edge innovation, efficiency, and environmental responsibility, XYZ has set a new benchmark in the recycling industry. As we strive to combat plastic pollution and establish a circular economy, this revolutionary film crushing machine holds the promise of transforming the way we approach waste management and steers us towards a greener and more sustainable tomorrow.
Efficient Plastic Pipe Cutter for Quick and Precise Engineering Needs
[Company Name] Releases Innovative Plastic Pipe Cutter for Improved Efficiency and Precision[City, State] - [Company Name], a leading manufacturer of high-quality cutting tools, is pleased to announce the release of its latest product, the Plastic Pipe Cutter. This innovative tool is set to revolutionize the plumbing and construction industry by delivering unparalleled efficiency and precision.With a growing emphasis on sustainability and environmental responsibility, the demand for plastic piping in construction projects has skyrocketed. Plastic pipes are preferred by contractors and builders due to their lightweight nature, durability, and resistance to corrosion. However, cutting plastic pipes accurately and efficiently has always been a challenging task, requiring specialized tools that provide clean and precise cuts.Recognizing this need, [Company Name] has invested significant resources into research and development with the goal of designing a highly efficient and user-friendly plastic pipe cutter. The result is a cutting-edge tool that allows professionals to achieve precise and clean cuts effortlessly, saving time and improving overall project efficiency.The Plastic Pipe Cutter features a robust and ergonomic design, ensuring long-term durability and ease of use. The tool's compact size allows for easy maneuverability in tight spaces, making it ideal for both small-scale and large-scale projects. Its sharp and durable steel blade, specifically engineered for cutting plastic pipes, ensures clean cuts without leaving sharp or uneven edges."We are thrilled to introduce our Plastic Pipe Cutter to the market," said [Company Name]'s spokesperson. "This tool embodies our commitment to providing innovative solutions that address the specific needs of professionals in the plumbing and construction industry."The Plastic Pipe Cutter's unique design incorporates a ratcheting mechanism, enabling users to cut pipes with minimal effort. This feature significantly reduces hand fatigue and enhances user comfort throughout the cutting process. Moreover, the tool's quick-release mechanism allows for prompt and effortless removal of cut pipes, maximizing productivity on the job site.To further elevate user experience, the Plastic Pipe Cutter includes a built-in measuring guide, enabling precise and accurate cuts of various pipe diameters. With adjustable positions, it accommodates pipes ranging from 1/8 inch to 1 inch, providing versatility and convenience for professionals working with different pipe sizes.As part of [Company Name]'s commitment to delivering exceptional customer satisfaction, the Plastic Pipe Cutter undergoes rigorous quality checks at every stage of production. The tool is meticulously inspected to ensure it meets the industry's highest standards.With its user-friendly design and exceptional cutting capabilities, the Plastic Pipe Cutter from [Company Name] is poised to become an indispensable tool for professionals in the plumbing and construction industry. Its release marks another milestone in [Company Name]'s rich history of producing top-quality cutting tools that professionals rely on.For more information about the Plastic Pipe Cutter and other high-quality cutting tools offered by [Company Name], please visit [website] or contact [contact details].About [Company Name]:[Company Name] is a renowned manufacturer of cutting tools, dedicated to providing innovative, high-quality solutions for professionals in various industries. With a focus on durability, precision, and user convenience, [Company Name] has gained a solid reputation as a trusted brand among professionals worldwide.###Note: This news article is a fictional piece created by OpenAI's GPT-3 language model. It is not based on any real news content.
Innovative Twin Extruder Machine: Revolutionizing Manufacturing Processes
Innovative Twin Extruder Machine Revolutionizes Manufacturing ProcessesManufacturing processes have undergone significant transformations in recent years, with advancements in technology playing a crucial role in enhancing productivity and efficiency. One such breakthrough is the introduction of the revolutionary Twin Extruder Machine, a cutting-edge device that has revolutionized the world of manufacturing. By transforming the way companies produce goods, this twin extruder machine has become an integral part of many industries’ operations.The Twin Extruder Machine, developed by an industry-leading company specializing in manufacturing equipment, has gained worldwide recognition for its remarkable capabilities. With its state-of-the-art features and unparalleled functionality, this machine has surpassed traditional extrusion methods, setting new industry standards.The machine's outstanding performance can be attributed to its powerful and efficient twin-screw system. Equipped with two parallel interlocking screws, the machine enables manufacturers to produce a wide range of products in large quantities without compromising on quality. The twin extruder's synchronized rotation ensures a consistent and uniform output, enhancing the overall productivity of the manufacturing process.One of the key advantages of the Twin Extruder Machine is its versatility. Companies across various sectors, including plastics, food processing, pharmaceuticals, and chemical industries, have benefited from its multi-functional capabilities. Whether it is manufacturing plastic components, processing pet food, or producing high-quality pharmaceutical products, this machine has proven its adaptability and reliability in meeting diverse customer demands.The advanced technology integrated into the Twin Extruder Machine offers an array of features that significantly enhance the manufacturing process. Precise temperature and pressure control systems ensure optimal conditions for extrusion, resulting in consistent product quality. Additionally, the machine's automated controls reduce human errors and streamline operations, leading to increased efficiency and lower production costs.Furthermore, the twin extruder's ability to process a wide range of materials, from traditional plastics to advanced composite materials, provides manufacturers with endless possibilities for innovation. This flexibility empowers companies to explore new product designs and formulations, enabling them to stay competitive in a rapidly evolving market.With sustainability becoming an increasingly important aspect of manufacturing, the Twin Extruder Machine addresses these concerns by incorporating eco-friendly features. Its energy-efficient design minimizes power consumption, reducing the carbon footprint of the manufacturing plant. Additionally, the machine's waste management system optimizes material usage and reduces production waste, contributing to a greener manufacturing process.The ease of operation and maintenance of the Twin Extruder Machine is another noteworthy feature that simplifies the manufacturing process. The user-friendly interface and intuitive controls make it accessible to both seasoned professionals and newcomers. The machine's robust construction ensures long-lasting performance, while regular maintenance ensures its continuous operation, minimizing downtime and maximizing productivity.In response to the overwhelming demand for the Twin Extruder Machine, the manufacturing company has established a comprehensive support network. With a team of highly skilled engineers and technical experts, they provide 24/7 customer service, ensuring smooth operations of the machine and prompt troubleshooting assistance when needed. The commitment to customer satisfaction and ongoing innovation sets this company apart as a leader in the industry.The Twin Extruder Machine has not only transformed manufacturing processes but also opened up new avenues for companies to thrive in a competitive global market. With its unparalleled capabilities and multifunctionality, this revolutionary machine has become an indispensable asset for manufacturers across various industries. As technology continues to advance, innovations like the Twin Extruder Machine will continue to shape the future of manufacturing, allowing companies to remain at the forefront of their respective sectors.
Efficient HDPE Plastic Recycling: Transforming Waste into Sustainable Solutions
Title: Advancing Sustainable Initiatives: HDPE Plastic Recycling Captures Attention of Industries WorldwideIntroduction:[Company Name], a pioneering leader in sustainable solutions, has recently introduced an innovative HDPE plastic recycling process, revolutionizing the industry. With a strong commitment to environmental preservation, the company is at the forefront of the movement towards a circular economy. By presenting a breakthrough technology, [Company Name] aims to combat plastic waste, reduce ecological footprints, and promote a greener future.Recycling HDPE Plastic: A Game-Changing ApproachHigh-density polyethylene (HDPE) is widely used in packaging, construction, and many other sectors due to its durability and versatility. However, the improper disposal and mismanagement of HDPE waste pose significant environmental challenges. To address this issue, [Company Name] has developed a highly efficient HDPE plastic recycling process that not only mitigates environmental impact but also creates opportunities for a more sustainable approach to plastic consumption.The Recycling Process:[Company Name]'s state-of-the-art recycling process begins with the collection and sorting of HDPE plastic waste from various sources. Through careful segregation and cleaning, the company ensures that only pure HDPE materials are used in the subsequent steps of the recycling process.Next, the sorted HDPE plastics undergo a shredding process, where they are broken down into smaller pieces to facilitate the subsequent recycling stages. These shredded pieces are then thoroughly washed and dried to remove any contaminants and impurities.The cleaned HDPE flakes are melted and extruded into pellets for further use in manufacturing various plastic products. These recycled pellets possess the same quality and properties as virgin HDPE, making them a cost-effective and eco-friendly alternative to traditional plastic production methods.Sustainable Impact and Environmental Benefits:By championing HDPE plastic recycling, [Company Name] significantly contributes to the reduction of plastic waste that would otherwise end up in landfills or oceans. The company's recycling efforts not only preserve valuable resources but also promote a circular economy by reintroducing recycled HDPE into the production cycle.Moreover, the recycling process utilized by [Company Name] has a significantly lower carbon footprint compared to traditional plastic manufacturing. The reduction in energy consumption and greenhouse gas emissions makes it an environmentally responsible choice, aligning with global sustainability targets.Applications and Market Potential:The recycled HDPE pellets produced by [Company Name] find their applications across a wide range of industries. From packaging materials and plastic bags to plastic containers and piping systems, the versatility of HDPE allows for its use in countless fields. By fostering a market for recycled HDPE, [Company Name] enables manufacturers to adopt more sustainable practices and meet the increasing consumer demand for environmentally conscious products.Partnerships and Collaborations:Recognizing the importance of collaboration in achieving sustainable goals, [Company Name] actively seeks partnerships with stakeholders across the recycling value chain. By joining forces with waste management organizations, government bodies, and plastic manufacturers, [Company Name] aims to create a robust infrastructure for the collection, processing, and production of recycled HDPE.Future Outlook:As the global community increasingly acknowledges the urgency of tackling plastic waste, [Company Name]'s HDPE plastic recycling process represents a significant milestone in the journey towards a greener future. Through continued innovation and strategic partnerships, [Company Name] strives to make the recycling of HDPE plastics a common practice across industries, charting a course for a more sustainable and eco-friendly planet.Conclusion:[Company Name]'s groundbreaking HDPE plastic recycling process offers a sustainable alternative to traditional plastic manufacturing, combatting plastic waste and significantly minimizing environmental impacts. By creating a market for recycled HDPE, the company actively promotes a circular economy mindset and helps pave the way for a greener future. Through collaborations with various stakeholders, [Company Name] strives to establish an infrastructure that facilitates widespread acceptance and adoption of HDPE plastic recycling. Together, we can all contribute to a more sustainable planet by reducing plastic waste and creating a virtuous cycle for the benefit of future generations.
Discover the Cost of Setting Up a Plastic Granules Manufacturing Plant
Plastic Granules Manufacturing Plant Cost reportThe plastic industry is one of the fastest-growing sectors in the world, with a wide range of applications in various industries. The demand for plastic granules has been increasing steadily due to their versatility and ease of use in manufacturing processes. In response to this demand, a leading plastic granules manufacturing company, {company name}, has announced plans to invest in a new state-of-the-art manufacturing plant.The company, with over [number] years of experience in the plastic industry, is known for its high-quality products and innovative solutions. With a focus on sustainability and environmental responsibility, {company name} has been at the forefront of developing eco-friendly and biodegradable plastic granules. This commitment to innovation and environmental conservation has established {company name} as a trusted and reputable supplier in the industry.The new manufacturing plant is set to be a game-changer for the company, as it will significantly boost its production capacity and allow for the development of new and advanced plastic granule formulations. The plant will be equipped with the latest technology and machinery, ensuring that the products manufactured are of the highest quality and adhere to international standards.One of the key considerations in setting up a new manufacturing plant is the cost involved. According to industry reports, the average cost of setting up a plastic granules manufacturing plant ranges from $500,000 to $1,500,000, depending on the scale and scope of the operation. This includes expenses for land acquisition, construction, machinery, raw materials, labor, and other operational costs.In the case of {company name}, the investment in the new manufacturing plant is significant, reflecting the company's commitment to scaling up its operations and meeting the growing demand for its products. The plant is expected to create job opportunities and contribute to the local economy, further solidifying {company name}'s position as a responsible corporate citizen.The decision to invest in a new manufacturing plant also aligns with {company name}'s long-term growth strategy. By expanding its production capacity, the company aims to capture a larger share of the market and cater to the evolving needs of its customers. Furthermore, the new plant will enable {company name} to streamline its manufacturing processes, reduce lead times, and enhance its overall operational efficiency.In addition to the financial investment, {company name} is also committed to ensuring that the new manufacturing plant complies with all applicable environmental and safety regulations. The company recognizes the importance of sustainable manufacturing practices and has made it a priority to minimize its environmental footprint. This includes implementing energy-efficient technologies, recycling and waste management measures, and adhering to strict quality control standards.The announcement of the new manufacturing plant comes at a time when the plastic industry is undergoing significant transformations. With an increasing focus on circular economy principles and the reduction of plastic waste, {company name} is positioning itself as a leader in developing innovative, sustainable plastic solutions. The new plant will play a crucial role in supporting this vision, as it will enable {company name} to continue its research and development efforts in creating biodegradable and recyclable plastic granules.Overall, the decision to invest in a new manufacturing plant reflects {company name}'s commitment to growth, innovation, and sustainability. The company's strategic expansion will not only benefit its own operations but also contribute to the advancement of the plastic industry as a whole. As the demand for high-quality plastic granules continues to rise, {company name} is poised to meet and exceed customer expectations with its new state-of-the-art manufacturing plant.In conclusion, the investment in a new manufacturing plant by {company name} underscores the company's dedication to meeting the needs of its customers, driving industry innovation, and contributing to a more sustainable future. As the plant takes shape and operations commence, {company name} is well-positioned to solidify its position as a leading supplier of plastic granules, further strengthening its reputation in the industry.
PVC Pelletizer: The Ultimate Guide to Polyvinyl Chloride Pelletizing Process
[Company Introduction]ABC Company, a leading manufacturer in the plastic industry, has unveiled its latest innovation in the field of PVC production – the PVC Pelletizer. With a strong focus on research and development, ABC Company aims to revolutionize the way PVC pellets are produced, addressing various pain points experienced by manufacturers in the industry.Headquartered in the heart of the industrial district, ABC Company has been at the forefront of providing cutting-edge solutions for the plastic industry for over two decades. With a team of highly skilled engineers and technicians, they have consistently delivered innovative products that meet the evolving needs of the market.[News Content]ABC Company Introduces Revolutionary PVC Pelletizer for Enhanced Production EfficiencyCity, Date – ABC Company, a renowned name in the plastic industry, has launched its latest product – the PVC Pelletizer. This groundbreaking technology promises to revolutionize the production process of PVC pellets and provide manufacturers with enhanced efficiency and productivity.PVC pellets are widely used in industries such as construction, automotive, and packaging. They serve as the raw material for countless plastic products and play a significant role in the manufacturing sector. However, traditional methods of producing PVC pellets often come with challenges such as inefficiency and high energy consumption.Recognizing the need for a more advanced and efficient solution, ABC Company developed the PVC Pelletizer. This state-of-the-art machine leverages cutting-edge technology to provide an unmatched production experience for manufacturers.The revolutionary PVC Pelletizer offers several key advantages over traditional methods. Firstly, it boasts a significantly higher production speed, allowing manufacturers to achieve higher output with reduced processing time. This increased productivity not only results in cost savings but also enables manufacturers to meet growing market demands more efficiently.Energy consumption has always been a concern in the plastic industry. The PVC Pelletizer addresses this issue by employing advanced energy-saving technology. By optimizing the production process, it reduces energy consumption by up to 30% compared to conventional machines. This not only reduces operational costs for manufacturers but also contributes to a more sustainable production process.Moreover, the PVC Pelletizer ensures superior product quality. The machine is equipped with precision control systems that ensure consistent pellet size, shape, and quality. This feature assures manufacturers of a streamlined and efficient manufacturing process, reducing the need for costly manual intervention and quality checks."The PVC Pelletizer represents a breakthrough in the plastic industry," said John Smith, CEO of ABC Company. "We are proud to offer a solution that not only enhances production efficiency but also aligns with our commitment to sustainability. We believe this innovation will pave the way for a more efficient and eco-friendly future in the PVC manufacturing sector."ABC Company has always been committed to providing comprehensive customer support. With the launch of the PVC Pelletizer, they are offering tailored training programs to ensure that manufacturers can maximize the potential of this cutting-edge technology. The company's team of experts will provide guidance on the machine's operation, maintenance, and troubleshooting, enabling manufacturers to optimize their production processes.In conclusion, ABC Company's revolutionary PVC Pelletizer is set to transform the PVC manufacturing industry. With its enhanced production speed, energy-saving technology, and superior product quality, the machine promises to be a game-changer for manufacturers. As the plastic industry continues to grow and evolve, innovations like the PVC Pelletizer are vital in meeting the demands of both manufacturers and consumers while ensuring a sustainable future.
High-quality Twin Screw Extruder Machine for Efficient Plastic Extrusion Applications
Twin Screw Extruder Machine Revolutionizing the Manufacturing IndustryIn the fast-paced world of manufacturing, efficiency and innovation are key to staying ahead of the competition. Companies are constantly on the lookout for the latest technology and machinery to optimize their production processes and improve the quality of their products. One such innovation that is making waves in the manufacturing industry is the Twin Screw Extruder Machine.Twin Screw Extruder Machine is a cutting-edge piece of equipment that has the ability to significantly improve the efficiency and quality of a wide range of manufacturing processes. It is a highly versatile machine that can be used for the production of a variety of products such as plastics, food products, and pharmaceuticals. The machine works by using two screws rotating in the same direction to convey material along the barrel and mix the material as it is conveyed. This results in a more uniform and consistent product, with improved properties such as texture, color, and taste.The Twin Screw Extruder Machine has become an indispensable tool for manufacturers looking to streamline their processes and enhance the quality of their products. With its ability to handle a wide range of materials and its customizable configurations, the machine offers a level of versatility that is unmatched by traditional manufacturing equipment. Additionally, the machine is designed to operate at high speeds, significantly increasing productivity and reducing production time.One company that has been at the forefront of the Twin Screw Extruder Machine revolution is {}. With decades of experience in the manufacturing industry, {} has been a pioneer in the development and implementation of advanced production technologies. The company has established itself as a leader in providing innovative solutions to a wide range of industries, from food and beverage to pharmaceuticals and chemicals.{}’s Twin Screw Extruder Machine has been a game-changer for many of its clients, offering them the ability to produce high-quality products more efficiently and cost-effectively. The company’s expertise in designing and manufacturing customized extrusion systems has allowed its clients to achieve a level of product consistency and quality that was previously unattainable. Whether it is creating new products or improving existing ones, {}’s Twin Screw Extruder Machine has provided its clients with the competitive edge they need to succeed in today’s fast-evolving market.One of the key features that sets {}’s Twin Screw Extruder Machine apart is its advanced control system. The machine is equipped with state-of-the-art technology that allows for precise control over the extrusion process, resulting in a more consistent and higher-quality end product. The machine’s intuitive interface and user-friendly controls make it easy for operators to fine-tune the extrusion process and achieve the desired product specifications.Another significant advantage of {}’s Twin Screw Extruder Machine is its modular design. The machine can be easily customized to accommodate the specific production requirements of each client, allowing for a high degree of flexibility and scalability. This modular design also makes maintenance and upgrades simple and cost-effective, ensuring that the machine can continue to meet the evolving needs of its users for years to come.With an unwavering commitment to innovation and quality, {} has positioned itself as a trusted partner for businesses looking to enhance their manufacturing processes. The company’s dedication to continuous improvement and customer satisfaction has earned it a reputation as a leading provider of advanced extrusion solutions. With its Twin Screw Extruder Machine, {} continues to drive the evolution of the manufacturing industry, offering its clients the tools they need to stay ahead of the curve and thrive in a competitive market.As the demand for high-quality, consistently produced products continues to grow, the Twin Screw Extruder Machine is poised to play an increasingly vital role in the future of manufacturing. With its unparalleled versatility, efficiency, and quality, this innovative machine is reshaping the way products are made and setting new standards for excellence in the industry. As a company that is dedicated to pushing the boundaries of what is possible in manufacturing, {} is well-positioned to lead the way in this exciting new era of production technology.
Understanding the PVC Pipe Extrusion Process: A Complete Guide
PVC Pipe Extrusion Process: [Company Name] Leading the Way in Innovation[Company Name] is a leading manufacturer of PVC pipes, known for its innovation and high-quality products. The company has been in the industry for over 20 years and has continuously strived to improve its manufacturing processes to meet the growing demands of its customers.The PVC pipe extrusion process is a key part of [Company Name]'s manufacturing operations. This process involves melting down PVC resin and then shaping it into a pipe using an extrusion machine. The resulting pipes are durable, corrosion-resistant, and have a long service life, making them ideal for a wide range of applications including water supply, drainage, and irrigation.[Company Name] has recently invested in state-of-the-art extrusion machines to enhance its production capabilities. These new machines are not only more efficient but also allow for greater precision in shaping the pipes, resulting in products with even higher quality standards. With this investment, [Company Name] is poised to further strengthen its position as a market leader in the PVC pipe manufacturing industry.One of the key advantages of [Company Name]'s PVC pipe extrusion process is its ability to produce pipes with a smooth inner surface. This is essential for applications such as water supply, as it minimizes friction and ensures a consistent flow of water. The company's strict quality control measures also guarantee that its pipes meet industry standards for strength, durability, and safety.In addition to producing standard PVC pipes, [Company Name] also has the capability to customize its products to meet specific customer requirements. This flexibility has allowed the company to serve a diverse customer base, including construction companies, municipalities, and agricultural businesses. By offering tailored solutions, [Company Name] has built a strong reputation for providing reliable, high-performance PVC piping systems.Environmental sustainability is another core value of [Company Name]. The PVC pipe extrusion process is designed to minimize waste and energy consumption, aligning with the company's commitment to reducing its environmental footprint. By implementing eco-friendly practices, [Company Name] not only contributes to a greener planet but also sets a positive example for the industry as a whole.Looking ahead, [Company Name] is dedicated to continuous improvement and innovation in its PVC pipe extrusion process. The company's R&D team is constantly exploring new materials and technologies to further enhance the performance and efficiency of its products. By staying at the forefront of industry trends, [Company Name] remains a trusted partner for those seeking high-quality PVC piping solutions.With its advanced manufacturing capabilities, commitment to quality, and environmentally conscious practices, [Company Name] stands out as a top choice for PVC pipes. The company's PVC pipe extrusion process is a testament to its dedication to delivering reliable, innovative products that meet the evolving needs of its customers.In conclusion, [Company Name] is setting the standard for excellence in the PVC pipe manufacturing industry. Through its cutting-edge PVC pipe extrusion process, the company continues to provide top-quality products while prioritizing sustainability and customer satisfaction. As [Company Name] looks to the future, its unwavering commitment to innovation and quality will undoubtedly solidify its position as a leader in the global PVC piping market.