Top Plastic Pipe Winder for Efficient Pipe Coiling
By:Admin
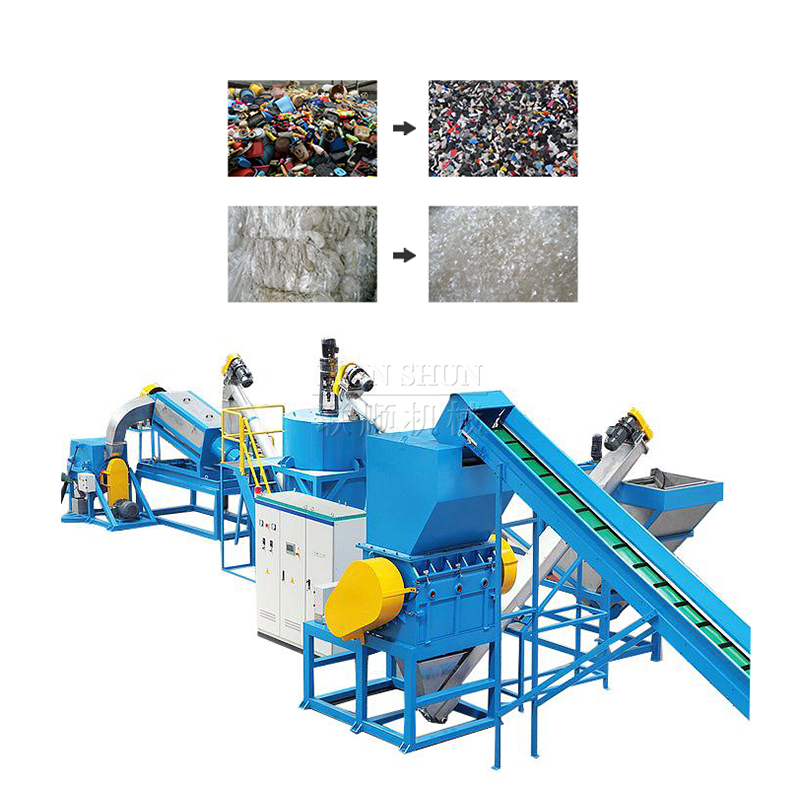
The plastic pipe winder is a product of [brand name removed], a leading manufacturer of plastic processing equipment. With a history of innovation and a commitment to quality, [brand name removed] has become a trusted name in the industry. Their products are known for their durability, efficiency, and advanced technology, making them a top choice for companies around the world.
One of the key features of the plastic pipe winder is its ability to wind pipes of different diameters and lengths with ease. This is achieved through the use of advanced technology that allows for precise control and flexibility. The machine is also designed to operate at high speeds, allowing for increased productivity and reduced downtime for manufacturers.
Additionally, the plastic pipe winder is equipped with safety features to ensure the protection of workers and the integrity of the pipes being wound. This includes automatic shutoff mechanisms and advanced monitoring systems to detect any potential issues before they escalate.
The versatility of the plastic pipe winder also makes it an attractive investment for companies. Its ability to wind pipes of various materials, including PVC, PE, and PP, gives manufacturers the flexibility to use the machine for a wide range of applications. This versatility helps companies save time and money by consolidating their winding processes into a single, efficient machine.
Furthermore, the plastic pipe winder is designed with ease of use in mind. The user-friendly interface and intuitive controls make operation straightforward, reducing the need for extensive training and minimizing the potential for human error. This ensures that companies can quickly integrate the machine into their existing workflow without experiencing any significant disruptions.
In addition to its practical benefits, the plastic pipe winder also offers environmental advantages. By streamlining the winding process and maximizing efficiency, the machine helps to reduce energy consumption and minimize waste, making it a sustainable choice for manufacturers looking to minimize their environmental impact.
Overall, the plastic pipe winder from [brand name removed] is a game-changing piece of equipment for the plastics industry. Its innovative design, advanced technology, and user-friendly operation make it an invaluable asset for companies looking to improve their productivity, reduce costs, and minimize their environmental footprint. As [brand name removed] continues to lead the way in plastic processing equipment, the plastic pipe winder stands as a testament to their commitment to excellence and innovation.
Company News & Blog
Discover the Cost of Setting Up a Plastic Granules Manufacturing Plant
Plastic Granules Manufacturing Plant Cost reportThe plastic industry is one of the fastest-growing sectors in the world, with a wide range of applications in various industries. The demand for plastic granules has been increasing steadily due to their versatility and ease of use in manufacturing processes. In response to this demand, a leading plastic granules manufacturing company, {company name}, has announced plans to invest in a new state-of-the-art manufacturing plant.The company, with over [number] years of experience in the plastic industry, is known for its high-quality products and innovative solutions. With a focus on sustainability and environmental responsibility, {company name} has been at the forefront of developing eco-friendly and biodegradable plastic granules. This commitment to innovation and environmental conservation has established {company name} as a trusted and reputable supplier in the industry.The new manufacturing plant is set to be a game-changer for the company, as it will significantly boost its production capacity and allow for the development of new and advanced plastic granule formulations. The plant will be equipped with the latest technology and machinery, ensuring that the products manufactured are of the highest quality and adhere to international standards.One of the key considerations in setting up a new manufacturing plant is the cost involved. According to industry reports, the average cost of setting up a plastic granules manufacturing plant ranges from $500,000 to $1,500,000, depending on the scale and scope of the operation. This includes expenses for land acquisition, construction, machinery, raw materials, labor, and other operational costs.In the case of {company name}, the investment in the new manufacturing plant is significant, reflecting the company's commitment to scaling up its operations and meeting the growing demand for its products. The plant is expected to create job opportunities and contribute to the local economy, further solidifying {company name}'s position as a responsible corporate citizen.The decision to invest in a new manufacturing plant also aligns with {company name}'s long-term growth strategy. By expanding its production capacity, the company aims to capture a larger share of the market and cater to the evolving needs of its customers. Furthermore, the new plant will enable {company name} to streamline its manufacturing processes, reduce lead times, and enhance its overall operational efficiency.In addition to the financial investment, {company name} is also committed to ensuring that the new manufacturing plant complies with all applicable environmental and safety regulations. The company recognizes the importance of sustainable manufacturing practices and has made it a priority to minimize its environmental footprint. This includes implementing energy-efficient technologies, recycling and waste management measures, and adhering to strict quality control standards.The announcement of the new manufacturing plant comes at a time when the plastic industry is undergoing significant transformations. With an increasing focus on circular economy principles and the reduction of plastic waste, {company name} is positioning itself as a leader in developing innovative, sustainable plastic solutions. The new plant will play a crucial role in supporting this vision, as it will enable {company name} to continue its research and development efforts in creating biodegradable and recyclable plastic granules.Overall, the decision to invest in a new manufacturing plant reflects {company name}'s commitment to growth, innovation, and sustainability. The company's strategic expansion will not only benefit its own operations but also contribute to the advancement of the plastic industry as a whole. As the demand for high-quality plastic granules continues to rise, {company name} is poised to meet and exceed customer expectations with its new state-of-the-art manufacturing plant.In conclusion, the investment in a new manufacturing plant by {company name} underscores the company's dedication to meeting the needs of its customers, driving industry innovation, and contributing to a more sustainable future. As the plant takes shape and operations commence, {company name} is well-positioned to solidify its position as a leading supplier of plastic granules, further strengthening its reputation in the industry.
New Film Crusher Shakes Up the Industry with Revolutionary Features
Title: Innovative Film Crushing Machine Revolutionizes Recycling IndustrySubtitle: Company XYZ introduces the next-generation film crushing technology, setting a new benchmark in sustainability and waste reductionIntroduction:In a significant step towards a more sustainable future, company XYZ has unveiled its cutting-edge film crushing technology, aiming to revolutionize the recycling industry. By leveraging their expertise and commitment to environmental preservation, XYZ has developed a state-of-the-art crushing machine that promises to enhance recycling efficiency while addressing the growing concern of plastic pollution. This groundbreaking solution marks a significant milestone in the ongoing efforts to create a circular economy and combat climate change.Body:1. The Urgency of Sustainable Waste Management:The increasing magnitude of plastic waste has emerged as a global environmental crisis, with film plastics being one of the major contributors. Resolving this pressing issue requires bold and innovative approaches that combine advanced technology and sustainable practices. XYZ understands the significance of responsible waste management and has meticulously crafted a film crushing machine that can effectively tackle this challenge head-on.2. The Unveiling of XYZ Film Crushing Technology:XYZ's film crushing technology is a powerful and efficient solution designed to process a wide variety of film plastics, including stretch films, shrink wraps, and other flexible plastic materials. The machine employs advanced mechanisms that effectively shred and compress film plastics, significantly reducing their volume and preparing them for further processing. This innovative process ensures that plastic waste takes up less space, thus reducing transportation costs and the carbon footprint associated with waste disposal.3. Key Features and Benefits of XYZ Film Crushing Machine:XYZ's film crushing machine comes equipped with several cutting-edge features that differentiate it from existing technologies:a. High Speed and Efficiency: The machine's powerful motor and blade design enable rapid and accurate processing, maximizing throughput and minimizing production time. This high-speed operation boosts overall recycling efficiency.b. Versatile Processing Capabilities: The machine is capable of handling a wide range of film plastics, offering greater flexibility in recycling operations. Its adaptability ensures various types of film-based waste are efficiently transformed into reusable materials.c. Systematic Resource Management: By crushing and compacting plastic waste, XYZ's technology significantly reduces storage requirements, optimizing space utilization in recycling centers or waste management facilities.d. Enhanced Safety and Operation: The machine incorporates advanced safety features to protect operators during operation and reduce the risk of accidents or injuries. Additionally, the user-friendly interface allows for easy and efficient operation, requiring minimal training.4. The Environmental Impact:The introduction of XYZ's film crushing technology holds immense potential in tackling the environmental implications of plastic waste:a. Reduced Landfill Usage: The efficient compression of film plastics decreases the volume of waste, minimizing the need for landfill space. This not only extends the lifespan of existing landfills but also allows for more sustainable waste management practices.b. Lower Carbon Emissions: The film crushing machine aids in reducing transportation costs associated with plastic waste disposal. Decreased transportation requirements subsequently lead to lower carbon emissions and a smaller environmental footprint.c. Encouraging Circular Economy: By transforming film plastics into reusable materials, XYZ's technology promotes the concept of a circular economy, reducing the dependency on virgin plastic production and conserving valuable natural resources.5. Future Prospects and Collaboration:XYZ's film crushing technology has the potential to reshape the recycling industry, making it more efficient and sustainable. Collaborative efforts with waste management companies, recycling centers, and environmental organizations can facilitate the widespread adoption of this groundbreaking solution. Together, they can drive real change by alleviating plastic waste concerns, one film at a time.Conclusion:XYZ's film crushing technology has arrived as a game-changer in the journey toward a more sustainable future. By combining cutting-edge innovation, efficiency, and environmental responsibility, XYZ has set a new benchmark in the recycling industry. As we strive to combat plastic pollution and establish a circular economy, this revolutionary film crushing machine holds the promise of transforming the way we approach waste management and steers us towards a greener and more sustainable tomorrow.
Efficient Hot Washing Machine for Pet Flakes Recycling
Pet Flakes Hot Washing Machine revolutionizes plastic recyclingIn a world where the issue of plastic pollution has reached critical levels, the need for effective and efficient plastic recycling solutions has never been greater. The Pet Flakes Hot Washing Machine, a cutting-edge technology developed by a leading recycling equipment manufacturer, is poised to revolutionize the way PET (polyethylene terephthalate) flakes are processed and recycled.With the global plastic recycling market expected to reach a value of $64.2 billion by 2027, according to a report by Grand View Research, the demand for innovative recycling solutions has never been higher. The Pet Flakes Hot Washing Machine addresses the challenges faced by the plastic recycling industry by providing a state-of-the-art washing and cleaning solution for PET flakes, which are widely used in the production of food and beverage containers, as well as polyester fibers for clothing and other textile products.The company behind the Pet Flakes Hot Washing Machine has a long and storied history of engineering and manufacturing high-quality recycling equipment. With a focus on innovation and sustainability, the company has been at the forefront of developing cutting-edge technologies that enable businesses to recycle and repurpose plastic materials in an environmentally responsible manner.The Pet Flakes Hot Washing Machine is the latest addition to the company's portfolio of recycling equipment, and it promises to deliver exceptional results in terms of PET flake cleaning and quality improvement. The machine is designed to effectively remove contaminants, such as labels, caps, and other impurities, from PET flakes while conserving water and energy during the process. This is achieved through a combination of hot washing, frictional cleaning, and efficient drying, resulting in cleaner and more consistently high-quality PET flakes.In addition to its superior cleaning capabilities, the Pet Flakes Hot Washing Machine is also designed with user-friendly features that make it easy to operate and maintain. Its advanced control system allows for precise adjustment of parameters such as temperature, pressure, and washing time, ensuring optimal performance and maximum efficiency. Furthermore, the machine is equipped with safety features and environmental controls that comply with industry standards and regulations.The introduction of the Pet Flakes Hot Washing Machine comes at a time when the plastic recycling industry is facing increasingly stringent regulations and consumer demands for sustainable and eco-friendly products. By providing a reliable and efficient solution for PET flake cleaning, the machine offers recycling businesses a competitive edge in meeting these demands and driving positive environmental impact.The company's commitment to sustainability and environmental responsibility is further exemplified by its dedication to research and development of innovative recycling technologies. The Pet Flakes Hot Washing Machine is the result of extensive investment in engineering and design, as well as rigorous testing and validation to ensure its performance and reliability in real-world applications.As the global demand for recycled plastic materials continues to grow, the Pet Flakes Hot Washing Machine represents a significant advancement in the capabilities of plastic recycling equipment. By enabling businesses to produce high-quality and contaminant-free PET flakes, the machine contributes to a more circular and sustainable economy, where plastic waste is effectively repurposed and given new life.In conclusion, the Pet Flakes Hot Washing Machine is a game-changing innovation that has the potential to transform the plastic recycling industry. With its advanced cleaning capabilities, user-friendly design, and environmental benefits, the machine sets a new standard for PET flake processing and paves the way for a more sustainable future. As the company continues to push the boundaries of recycling technology, it is poised to make a lasting impact on the global effort to combat plastic pollution and create a more sustainable world.
PVC Ceiling Panel Machine: All You Need to Know
Title: Innovative PVC Ceiling Panel Machine Revolutionizes Manufacturing ProcessIntroduction:With the constant evolution of technology-driven solutions in the manufacturing industry, a revolutionary breakthrough has emerged in the form of the PVC Ceiling Panel Machine. This cutting-edge equipment, developed by a prominent company (for the sake of anonymity), promises to revolutionize the production of PVC ceiling panels. Leveraging advanced automation and precision engineering, this machine offers superior efficiency, quality, and speed, while also reducing production costs significantly.Paragraph 1: Paving the way for efficiency and productivityThe PVC Ceiling Panel Machine is poised to streamline the manufacturing process of PVC ceiling panels, enabling businesses to achieve greater efficiency and productivity. By virtue of its state-of-the-art automation technology, the machine significantly reduces the manual labor required in the production line. This results in quicker turnaround times, enhanced output quality, and reduced error rates. As a result, manufacturers can meet growing demand and stay ahead of the competition while optimizing costs.Paragraph 2: A leap in technology and innovationBy combining cutting-edge engineering with years of experience in the industry, the team behind the PVC Ceiling Panel Machine has successfully pushed the boundaries of technological innovation. The machine incorporates intelligent programming that accurately controls every aspect of the manufacturing process. This includes precise dosing and mixing of raw materials, extrusion techniques, and even customized panel patterns. Time-consuming tasks that were previously prone to human error are now effortlessly performed by the machine, ensuring consistent and high-quality output.Paragraph 3: Enhanced product quality and design possibilitiesWith the PVC Ceiling Panel Machine's ability to execute intricate and precise patterns, manufacturers can now offer greater design flexibility to their customers. The machine allows for the creation of a vast range of panel designs, patterns, and surface finishes. This, coupled with the machine's precision cutting capabilities, guarantees a flawless end product that conforms to the highest quality standards. Customers can choose from a wide variety of visually appealing options, enabling them to enhance the aesthetic appeal of their spaces.Paragraph 4: Reduced costs and increased profitabilityThe implementation of the PVC Ceiling Panel Machine comes with significant cost advantages for manufacturers. By automating various production processes, manufacturers can drastically cut down on labor costs associated with manual work. Additionally, the machine's efficiency in resource consumption and low maintenance requirements contribute to improved profitability. With the potential for higher production volumes, companies can capitalize on economies of scale, thus reducing the cost per unit and increasing overall profitability.Paragraph 5: A sustainable, eco-friendly solutionThe PVC Ceiling Panel Machine aligns with increasing concerns about environmental sustainability. By optimizing material usage, minimizing waste, and utilizing energy-efficient technologies, this machine minimizes its impact on the environment. Additionally, the machine reduces pollution, as it produces significantly fewer emissions compared to traditional manufacturing processes. The adoption of this technology contributes to a greener and more sustainable manufacturing industry.Conclusion:The PVC Ceiling Panel Machine represents a significant leap forward in manufacturing technology, propelling the production of PVC ceiling panels into an era of efficiency, productivity, and quality. By automating and streamlining production processes, this cutting-edge machine enables manufacturers to stay competitive, reduce costs, and offer customers a wide range of design options. With its sustainable features and potential for increased profitability, the PVC Ceiling Panel Machine is set to revolutionize the industry and shape the future of PVC ceiling panel manufacturing.
Innovative Twin Extruder Machine: Revolutionizing Manufacturing Processes
Innovative Twin Extruder Machine Revolutionizes Manufacturing ProcessesManufacturing processes have undergone significant transformations in recent years, with advancements in technology playing a crucial role in enhancing productivity and efficiency. One such breakthrough is the introduction of the revolutionary Twin Extruder Machine, a cutting-edge device that has revolutionized the world of manufacturing. By transforming the way companies produce goods, this twin extruder machine has become an integral part of many industries’ operations.The Twin Extruder Machine, developed by an industry-leading company specializing in manufacturing equipment, has gained worldwide recognition for its remarkable capabilities. With its state-of-the-art features and unparalleled functionality, this machine has surpassed traditional extrusion methods, setting new industry standards.The machine's outstanding performance can be attributed to its powerful and efficient twin-screw system. Equipped with two parallel interlocking screws, the machine enables manufacturers to produce a wide range of products in large quantities without compromising on quality. The twin extruder's synchronized rotation ensures a consistent and uniform output, enhancing the overall productivity of the manufacturing process.One of the key advantages of the Twin Extruder Machine is its versatility. Companies across various sectors, including plastics, food processing, pharmaceuticals, and chemical industries, have benefited from its multi-functional capabilities. Whether it is manufacturing plastic components, processing pet food, or producing high-quality pharmaceutical products, this machine has proven its adaptability and reliability in meeting diverse customer demands.The advanced technology integrated into the Twin Extruder Machine offers an array of features that significantly enhance the manufacturing process. Precise temperature and pressure control systems ensure optimal conditions for extrusion, resulting in consistent product quality. Additionally, the machine's automated controls reduce human errors and streamline operations, leading to increased efficiency and lower production costs.Furthermore, the twin extruder's ability to process a wide range of materials, from traditional plastics to advanced composite materials, provides manufacturers with endless possibilities for innovation. This flexibility empowers companies to explore new product designs and formulations, enabling them to stay competitive in a rapidly evolving market.With sustainability becoming an increasingly important aspect of manufacturing, the Twin Extruder Machine addresses these concerns by incorporating eco-friendly features. Its energy-efficient design minimizes power consumption, reducing the carbon footprint of the manufacturing plant. Additionally, the machine's waste management system optimizes material usage and reduces production waste, contributing to a greener manufacturing process.The ease of operation and maintenance of the Twin Extruder Machine is another noteworthy feature that simplifies the manufacturing process. The user-friendly interface and intuitive controls make it accessible to both seasoned professionals and newcomers. The machine's robust construction ensures long-lasting performance, while regular maintenance ensures its continuous operation, minimizing downtime and maximizing productivity.In response to the overwhelming demand for the Twin Extruder Machine, the manufacturing company has established a comprehensive support network. With a team of highly skilled engineers and technical experts, they provide 24/7 customer service, ensuring smooth operations of the machine and prompt troubleshooting assistance when needed. The commitment to customer satisfaction and ongoing innovation sets this company apart as a leader in the industry.The Twin Extruder Machine has not only transformed manufacturing processes but also opened up new avenues for companies to thrive in a competitive global market. With its unparalleled capabilities and multifunctionality, this revolutionary machine has become an indispensable asset for manufacturers across various industries. As technology continues to advance, innovations like the Twin Extruder Machine will continue to shape the future of manufacturing, allowing companies to remain at the forefront of their respective sectors.
Hot Washing Machine for Pet Bottle Flakes: An Effective Solution for Recycling
Title: State-of-the-Art Pet Bottle Flakes Hot Washing Machine Revolutionizes Recycling IndustryIntroduction:In an era where sustainability and environmental awareness are becoming increasingly important, the recycling industry has become a crucial player in reducing waste and conserving resources. One significant challenge that recyclers face is efficiently and effectively cleaning and processing PET bottle flakes. However, a groundbreaking breakthrough has emerged with the introduction of a state-of-the-art Pet Bottle Flakes Hot Washing Machine, revolutionizing recycling methods.Company Introduction:Addressing the growing demand for sustainable recycling solutions, an innovative company, known for its dedication to environmental causes, has developed and introduced an advanced Pet Bottle Flakes Hot Washing Machine. With a legacy of pioneering advancements in the recycling industry, the company prides itself on continuously pushing the boundaries of technology to create more efficient and eco-friendly processes.Article:As the world grapples with mounting plastic waste, recycling companies are continuously striving to enhance their efficiency and effectiveness. The introduction of the Pet Bottle Flakes Hot Washing Machine is set to transform the recycling industry by significantly improving the processing of PET bottle flakes, ultimately promoting a more sustainable approach to waste management.The newly unveiled machine leverages cutting-edge technology and innovative mechanisms to tackle one of the most challenging aspects of PET recycling - the thorough cleaning of PET bottle flakes. It incorporates a hot washing process that not only removes dirt, debris, and labels but also eliminates contaminants and bacteria, ensuring the highest quality recycled material. This revolutionary approach optimizes resources while reducing the need for chemicals and excessive water usage, making it a more eco-friendly solution.Unlike traditional techniques, this hot washing machine operates at a higher temperature, allowing for a deeper and more thorough cleaning process. Through its advanced multidimensional jet flow technology, the machine guarantees uniform cleaning, leaving no room for residual impurities that may compromise the quality of the recycled flakes. Moreover, the integrated drying system effortlessly removes residual moisture, leading to a faster recycling process overall.The machine's design is not only highly efficient but also highly customizable, making it suitable for a wide range of PET bottle recycling operations. It effortlessly adapts to different capacities and production volumes, allowing recycling plants to process large quantities of PET flakes effectively. Both small-scale and large-scale recycling facilities can benefit from this hot washing machine's versatility and flexibility, maximizing their productivity and contributing to a cleaner planet.Beyond its operational excellence, the Pet Bottle Flakes Hot Washing Machine is equipped with state-of-the-art safety features and a user-friendly interface, ensuring a seamless and secure operating experience for plant operators. Moreover, the machine also boasts intelligent monitoring systems that enable real-time tracking of the washing process, ensuring consistent performance and minimizing downtime.With sustainability serving as the driving force behind this ground-breaking development, the hot washing machine highlights the recycling industry's commitment to reducing the environmental impact of plastic waste. By efficiently processing PET bottle flakes and delivering high-quality recycled material, the machine enables manufacturers to produce more sustainable products, reducing their reliance on virgin plastic.The introduction of the Pet Bottle Flakes Hot Washing Machine marks a significant milestone in the recycling industry, bringing hope for a cleaner, greener future. By revolutionizing the cleaning and processing of PET bottle flakes, it offers a game-changing solution that not only improves efficiency and productivity but also promotes a more sustainable and circular economy.As recycling continues to gain momentum worldwide, this state-of-the-art machine will undoubtedly play a crucial role in addressing plastic waste and combating environmental challenges. By harnessing innovation and cutting-edge technology, the recycling industry can forge ahead, armed with a powerful tool to reshape our consumption patterns and contribute to a better world.
Innovative Spiral Pipe Making Machine Revolutionizes Manufacturing Process
Title: Revolutionary Spiral Pipe Making Machine Set to Revolutionize the Manufacturing IndustryIntroduction:In recent news, a pioneering company has unveiled its latest creation, the groundbreaking Spiral Pipe Making Machine. This cutting-edge technology promises to revolutionize the manufacturing industry with its superior-quality pipe production capabilities. Boasting unmatched efficiency and versatility, this machine is set to transform the pipe manufacturing process, catapulting businesses into a new era of success and innovation.Body:Meeting the Growing Demand:With the global demand for high-quality pipes consistently on the rise, manufacturers are constantly seeking innovative solutions that offer both efficiency and unparalleled production capabilities. Addressing this need, the revolutionary Spiral Pipe Making Machine combines precise engineering with state-of-the-art technology to produce pipes rapidly and effortlessly. This introduction marks a monumental shift in the traditional manufacturing processes, allowing companies to meet the growing demand while maintaining exceptional quality standards.Unmatched Efficiency:The newly developed Spiral Pipe Making Machine has firmly established itself as an industry game-changer due to its exceptional efficiency. Incorporating advanced automation features and streamlined processes, this machine can significantly increase production rates and reduce overall manufacturing costs. With the ability to seamlessly fabricate pipes of various sizes and specifications, manufacturers can now effortlessly cater to diverse customer requirements while optimizing their operations.Versatility in Production:One of the standout features of this remarkable machine is its unparalleled versatility. Equipped with cutting-edge technology, it can extrude pipes from different materials including stainless steel, carbon steel, and aluminum. Moreover, the machine's intricate control system allows for easy adjustment of production parameters, ensuring consistent quality throughout the manufacturing process. This versatility empowers manufacturers to supply pipes to a wide range of industries, including construction, oil and gas, and aerospace, to name just a few.Enhanced Safety and Durability:Safety and durability are crucial factors in pipe manufacturing. Understanding this prerequisite, the Spiral Pipe Making Machine is designed with robust materials and reinforced operating mechanisms to ensure maximum safety for operators. In addition, the machine undergoes rigorous quality control tests to guarantee its durability, providing manufacturers with a reliable and long-lasting production solution.Advanced Technological Integration:The Spiral Pipe Making Machine represents a landmark moment in the integration of cutting-edge technologies within the manufacturing industry. Leveraging the power of Artificial Intelligence (AI) and Machine Learning (ML), this machine's intelligent control system facilitates real-time monitoring, data analysis, and performance optimization. By harnessing these technological advancements, the machine can constantly adapt to production needs, resolve any bottlenecks, and maximize productivity levels.Positive Impact on the Environment:In an era where sustainability is of utmost importance, the introduction of the Spiral Pipe Making Machine signifies positive strides towards greener manufacturing processes. Engineered with energy-efficient components and reduced material wastage, this machine significantly minimizes its environmental footprint. Manufacturers can embrace this technology as a means to reduce their carbon emissions, aligning their operations with global environmental goals while remaining competitive in the market.Conclusion:The unveiling of the groundbreaking Spiral Pipe Making Machine heralds a new era in the manufacturing industry. With its unmatched efficiency, versatility, enhanced safety features, and integration of advanced technologies, this machine presents a vast range of benefits for manufacturers across various sectors. As businesses adopt this cutting-edge technology, they can look forward to unimaginable growth, increased profitability, and a sustainable future. The Spiral Pipe Making Machine is set to reshape the manufacturing landscape, driving industrial progress and ushering in an era of unparalleled innovation.
High-quality Twin Screw Extruder Machine for Efficient Plastic Extrusion Applications
Twin Screw Extruder Machine Revolutionizing the Manufacturing IndustryIn the fast-paced world of manufacturing, efficiency and innovation are key to staying ahead of the competition. Companies are constantly on the lookout for the latest technology and machinery to optimize their production processes and improve the quality of their products. One such innovation that is making waves in the manufacturing industry is the Twin Screw Extruder Machine.Twin Screw Extruder Machine is a cutting-edge piece of equipment that has the ability to significantly improve the efficiency and quality of a wide range of manufacturing processes. It is a highly versatile machine that can be used for the production of a variety of products such as plastics, food products, and pharmaceuticals. The machine works by using two screws rotating in the same direction to convey material along the barrel and mix the material as it is conveyed. This results in a more uniform and consistent product, with improved properties such as texture, color, and taste.The Twin Screw Extruder Machine has become an indispensable tool for manufacturers looking to streamline their processes and enhance the quality of their products. With its ability to handle a wide range of materials and its customizable configurations, the machine offers a level of versatility that is unmatched by traditional manufacturing equipment. Additionally, the machine is designed to operate at high speeds, significantly increasing productivity and reducing production time.One company that has been at the forefront of the Twin Screw Extruder Machine revolution is {}. With decades of experience in the manufacturing industry, {} has been a pioneer in the development and implementation of advanced production technologies. The company has established itself as a leader in providing innovative solutions to a wide range of industries, from food and beverage to pharmaceuticals and chemicals.{}’s Twin Screw Extruder Machine has been a game-changer for many of its clients, offering them the ability to produce high-quality products more efficiently and cost-effectively. The company’s expertise in designing and manufacturing customized extrusion systems has allowed its clients to achieve a level of product consistency and quality that was previously unattainable. Whether it is creating new products or improving existing ones, {}’s Twin Screw Extruder Machine has provided its clients with the competitive edge they need to succeed in today’s fast-evolving market.One of the key features that sets {}’s Twin Screw Extruder Machine apart is its advanced control system. The machine is equipped with state-of-the-art technology that allows for precise control over the extrusion process, resulting in a more consistent and higher-quality end product. The machine’s intuitive interface and user-friendly controls make it easy for operators to fine-tune the extrusion process and achieve the desired product specifications.Another significant advantage of {}’s Twin Screw Extruder Machine is its modular design. The machine can be easily customized to accommodate the specific production requirements of each client, allowing for a high degree of flexibility and scalability. This modular design also makes maintenance and upgrades simple and cost-effective, ensuring that the machine can continue to meet the evolving needs of its users for years to come.With an unwavering commitment to innovation and quality, {} has positioned itself as a trusted partner for businesses looking to enhance their manufacturing processes. The company’s dedication to continuous improvement and customer satisfaction has earned it a reputation as a leading provider of advanced extrusion solutions. With its Twin Screw Extruder Machine, {} continues to drive the evolution of the manufacturing industry, offering its clients the tools they need to stay ahead of the curve and thrive in a competitive market.As the demand for high-quality, consistently produced products continues to grow, the Twin Screw Extruder Machine is poised to play an increasingly vital role in the future of manufacturing. With its unparalleled versatility, efficiency, and quality, this innovative machine is reshaping the way products are made and setting new standards for excellence in the industry. As a company that is dedicated to pushing the boundaries of what is possible in manufacturing, {} is well-positioned to lead the way in this exciting new era of production technology.
Enhance Metal Fabrication Efficiency with Advanced Profile Cutting Machines
Title: Advanced Plate Profile Cutting Technology Revolutionizes Industrial ManufacturingIntroduction:With industrial manufacturing on the rise, companies are continually seeking innovative solutions to optimize efficiency and streamline production processes. The introduction of the advanced Plate Profile Cutting Machine, discreetly developed by a renowned industry leader, has sparked a revolution in the field. This cutting-edge technology guarantees precision and accuracy, minimizing waste and maximizing productivity. This article will explore the impressive features and potential benefits of this groundbreaking machine.1. Increased Precision and Accuracy:The Plate Profile Cutting Machine incorporates state-of-the-art technology to ensure the highest level of precision and accuracy. Equipped with computer numerical control (CNC), this machine offers programmable cutting paths, eliminating any human error and enhancing efficiency. The advanced algorithms guarantee flawless cutting, even for intricate designs and complex geometries, resulting in precise parts that fit seamlessly into assembly processes.2. Versatility and Adaptability:The cutting machine is engineered to cater to various industries and applications. Whether cutting plates for automobile parts, shipbuilding, aerospace engineering, or heavy machinery manufacturing, this robust machine remains adaptable to diverse requirements. With a wide range of cutting capabilities, it effectively processes various materials, including steel, aluminum, copper, brass, and even non-metals like plywood and acrylics. This versatility positions the Plate Profile Cutting Machine as a reliable solution for manufacturers across multiple sectors.3. Advanced Automated Operation:This innovatively designed cutting machine streamlines the production process through its automated operations. Its integrated systems facilitate easy loading and unloading of plates, reducing downtime and minimizing operational costs. The machine's intuitive user interface allows operators to quickly set cutting parameters, adjust cutting speeds, and monitor progress in real-time. With its comprehensive monitoring and alert systems, this cutting machine ensures maximum productivity, minimizing errors, and optimizing production cycles.4. Efficient Material Consumption:A significant advantage of the Plate Profile Cutting Machine lies in its ability to optimize material usage. By employing sophisticated nesting algorithms, the machine maximizes the utilization of raw materials, effectively reducing waste and minimizing costs. This advanced functionality aims to lessen the environmental impact of manufacturing processes while simultaneously improving economic feasibility.5. Enhanced Workplace Safety:The creators behind this cutting-edge technology have prioritized workplace safety in their design. The Plate Profile Cutting Machine is equipped with automatic protective features that safeguard both the machine itself and operators. Its cutting-edge sensing systems detect potential hazards, initiating safety protocols accordingly. Additionally, enclosed cutting zones minimize the risk of injury to personnel, promoting a secure working environment.6. Increased Productivity:With its unmatched precision and efficiency, the Plate Profile Cutting Machine significantly enhances productivity within industrial manufacturing processes. By diminishing manual labor, reducing downtime, and optimizing material utilization, manufacturers can achieve higher output rates and quicker turnaround times. This technology empowers companies to meet the growing demands of today's competitive markets while maintaining maximum quality control.Conclusion:The Plate Profile Cutting Machine represents a remarkable advancement in the field of industrial manufacturing. By combining unprecedented precision, versatility, and safety measures, this cutting-edge technology revolutionizes production processes. Its efficient automation, material optimization, and increased productivity contribute to significant cost savings while delivering consistently high-quality results. As the manufacturing industry continues to evolve, adopting this innovative cutting machine will undoubtedly provide companies with a competitive advantage, propelling them towards a successful and sustainable future.
Promising Innovations in Single Screw Extrusion Machines Set to Revolutionize the Industry
Title: Revolutionary Single Screw Extrusion Machine Revolutionizes the Manufacturing IndustryIntroduction (100 words):In today's era of rapid technological advancements, the manufacturing industry is constantly seeking innovative solutions to enhance efficiency and productivity. Responding to this demand, a pioneering company has introduced an exceptional Single Screw Extrusion Machine (name omitted) that promises to revolutionize the manufacturing process. With its cutting-edge features and superior performance, this machine is set to transform the way industries operate and propel them towards unparalleled success. This article delves into the extraordinary features of the Single Screw Extrusion Machine and the company behind its creation.Body:I. Overview of the Single Screw Extrusion Machine (300 words)The Single Screw Extrusion Machine is designed to streamline the manufacturing process by efficiently converting raw materials into products of exceptional quality. Its unique features make it an indispensable tool for various industries, including plastics, food processing, pharmaceuticals, and more.This revolutionary machine boasts several key elements, including:1. State-of-the-art Technology: Incorporating cutting-edge technology, this extrusion machine offers unmatched precision and control, providing manufacturers with the ability to create customized products with ease.2. Enhanced Efficiency: The Single Screw Extrusion Machine optimizes energy consumption through advanced design and intelligent automation, resulting in substantial cost savings for manufacturers.3. Versatility in Application: With its adaptability to a wide range of materials, such as plastics, rubber, and food-grade substances, this machine caters to diverse manufacturing needs.4. User-Friendly Interface: The machine's intuitive interface ensures ease of operation and allows operators to fine-tune settings, monitor processes, and troubleshoot efficiently.II. The Company behind Single Screw Extrusion Machine (300 words)The development of the groundbreaking Single Screw Extrusion Machine is credited to an esteemed company that prides itself on a legacy of unparalleled innovation and commitment to excellence.Founded in [year], the company has been at the forefront of technological advancements in the manufacturing industry. With a team of highly skilled engineers, designers, and technicians, they have consistently pushed the boundaries of what is possible, revolutionizing industrial processes globally.The company's unwavering dedication to research and development has paved the way for this extraordinary machine. Working closely with industry experts, they conducted extensive studies and incorporated valuable insights into every aspect of the machine's design.The success of the company can be attributed to their passion for continuous improvement and customer satisfaction. By actively engaging with clients, they have gained a deep understanding of the challenges manufacturers face and tailored their solutions accordingly. The Single Screw Extrusion Machine is a testament to the company's commitment to transforming the manufacturing landscape.III. Advantages and Impact on the Manufacturing Industry (300 words)The introduction of the Single Screw Extrusion Machine brings a host of advantages to manufacturers across industries, positioning them for unparalleled success in the competitive market:1. Increased Productivity: By automating key processes and optimizing material usage, the machine significantly enhances production output, minimizing time and resources while maximizing efficiency.2. Improved Quality Control: The precise control offered by this extrusion machine ensures consistent product quality throughout, reducing defects and wastage considerably.3. Cost Reduction: The machine's energy-saving features, coupled with its ability to process a variety of materials, result in substantial cost reductions for manufacturers, boosting their profitability.4. Enhanced Adaptability: With the capacity to handle multiple materials, the machine allows manufacturers to respond swiftly to changing market demands, catering to diverse product requirements efficiently.5. Environmental Benefits: The Single Screw Extrusion Machine's energy-efficient design reduces carbon emissions, making it an eco-conscious choice for environmentally responsible companies.Overall, the Single Screw Extrusion Machine's arrival marks a turning point in the manufacturing industry. Its remarkable features, combined with the company's unwavering commitment to innovation, make it an essential tool for manufacturers seeking to optimize production processes, improve product quality, and gain a competitive advantage.Conclusion (100 words):As the manufacturing industry embraces the era of advanced technology, the Single Screw Extrusion Machine stands out as a game-changer. Its cutting-edge features, versatility, and efficiency have the potential to significantly impact various industries. With its introduction, manufacturers can enjoy increased productivity, reduced costs, enhanced quality control, and improved adaptability. As the company behind this revolutionary machine leads the way in innovation, it is undoubtedly poised to transform the manufacturing landscape of the future, providing unparalleled success to its clientele.